15%. This is the average percentage of fabric that is thrown away when a textile item is cut out. And behind this figure, which is (too) high, is the waste of other resources: water in particular, energy, textile fibres and other waste, not to mention the products, sometimes toxic for the soil, that are used in the processes to manufacture clothing, bags or pairs of shoes.
At TopTex, we place great importance on the quality of our products, but never to the detriment of the environment. This is why we are committed to finding innovative solutions to reduce our environmental impact.
So, faced with the fact that some textiles are being wasted, we wanted to join an initiative that would allow us to reuse fabric scraps. The name of this initiative is the K-loop project.
This Kariban Brands project reflects the values of innovation, collaboration and eco-responsibility that we hold dear. And to go even further, it was essential to add transparency and traceability requirements.
We will explain everything!
The K-loop process, recycled materials for recovering waste
The K-loop project is a manufacturing process based on the recycling and recovery of materials that were going to be thrown away. This is what is known as the circular economy: in short, a virtuous loop!
The KARIBAN BRANDS Kimood brand is the first to introduce this original process to the TopTex Group’s brands. So how does the K-loop process work in practice?
First, cotton scraps from the manufacture of Kariban t-shirts are recovered. And where possible, these pieces of fabric are separated by colour. Then, all the recovered textile material is shredded so that becomes fibres again.
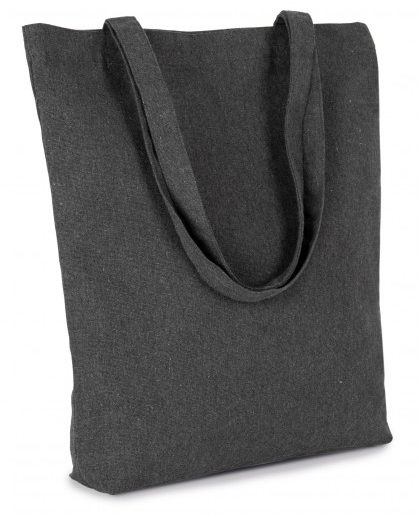
KI5808
Recycled cotton K-loop project shopper
Once these fibres have been recovered, they must be made longer and stronger, so they are interwoven with polyester. And this polyester comes from recyclable plastic bottles. As a result, these fibres can be woven back together again. This is the so-called K-loop.
Using these new yarns, Kimood designs KI5808 tote bags that are both strong AND eco-friendly!
The main idea of the K-loop project is to introduce a production process into a virtuous circle. Waste reduction, recycling and recovery: a cycle in which “nothing is lost, nothing is created, everything is transformed” (Antoine Lavoisier).
And that’s not all: to maximise the positive impact of this project, together with KARIBAN BRANDS, we wanted to give it even more scope.
Circular economy yes, but transparency too
Because this process could only exist if it was totally transparent and verifiable, Kimood worked on the possibility of tracing K-loop products. This concept of traceability means being able to retrace a product’s journey, from its origin to its distribution. Finally each bag made using the K-loop process will have its own “passport” which will contain unique, transparent and, above all, reliable information on the entire journey of each bag. How is this done? Using Aware, which designs traceability solutions for textile products, directly incorporated in the fibres.
Let’s take a look at the process: once the cotton scraps have been shredded and combined with recycled plastic, new fibres are obtained and ready to be woven. Then, during the weaving process, tiny particles are incorporated in the yarn. They will constitute a unique, unmodifiable digital fingerprint for each bag. This information can be scanned and viewed. It guarantees the origin of the materials, the true ecological impact and certifies that the item is genuinely recycled!
In addition, to ensure that this information is stored securely, Aware uses the famous blockchain: THE safest storage method, with no intermediaries and totally independent of any organisation, which prevents any modification of the data stored there. This data is thus tamper-proof, and will follow the product throughout its life, even if it undergoes further processing.
Kimood can therefore be sure that each bag will have its journey saved and secured “forever”: the guarantee of authenticity and honesty dear to the K-loop project!
And the K-loop is closed
As you can see, the KARIBAN BRANDS wanted to take care of every detail for this project. They are doing their utmost to incorporate greater respect for the environment and its resources in their businesses, and we are aware that we need to go even further to bring about change.
So the K-loop process is not just about fighting waste!
Above all, the desire is to move towards sustainable fashion, of course, but with concrete, tangible actions that have an impact at as many levels as possible:
1: Saving water and recovering fabrics that would have been thrown away
This is obviously the basis of the process: recovering unused scraps, and keeping their original colour to avoid having to dye them. Dyeing is a process that involves the use of water, energy and chemicals. So, to avoid this, the scraps are sorted by colour: the product designed using the recycled fibres will then be the same colour as the scraps. If the pieces of fabric are too small, or there are not enough to be sorted, they are all mixed together: this mixture is called “Jhoot”. Zero waste!
2: Incorporating some organic cotton
Whenever possible, organic cotton scraps from the production of KARIBAN BRANDS items are recovered. The cultivation of organic cotton is highly regulated and less harmful than that of traditional cotton: it requires less water and energy and avoids soil depletion caused by toxic products.
We therefore aim to make it our first choice in most cases, and we can maximise its impact even more by recycling it in the K-loop process.
3: Recycling plastic (PET)
We add polyester to lengthen and strengthen the recycled cotton yarns. It is made from plastic bottles that are crushed and transformed into fibres that can be woven. The aim is to give these bottles a second life and reduce the amount of plastic particles that unfortunately all too often end up in our oceans.
In addition, polyester fibres are flexible and strong, giving Kimood bags excellent durability.
4: Reducing the carbon footprint
The factories in which the Kimood bags are designed are just 20 km away from the KARIBAN BRANDS spinning centres (where the fabric scraps are recovered). So travel is reduced and optimised: less transport = lower carbon emissions! Having a short journey at this stage in the design process helps to further reduce the final environmental footprint of Kimood cotton tote bags.
5: Traceability of finished products
To make this process part of a genuine and certifiable approach, it is important to be able to prove the long-term commitment. The tracers incorporated in the yarn guarantee definitive storage of the information throughout the journey of the products.
As seen above, each passport is stored on the public blockchain, and contains precise information that cannot be modified: origin of the materials, energy saved, social responsibility, etc.
Kimood wanted to provide tangible proof of the responsible design of its KI5808 bags: this has been achieved with the Aware passports!
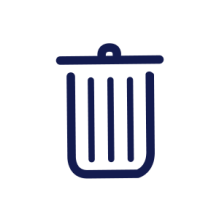
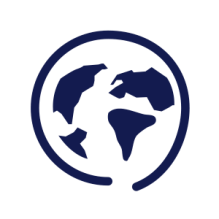
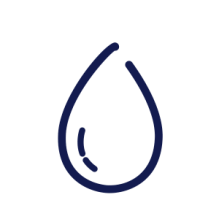
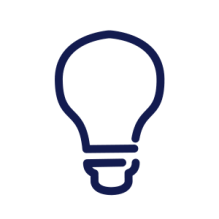
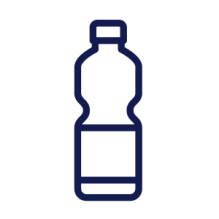
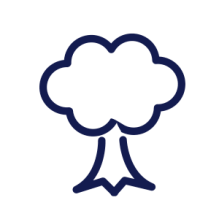
A collaborative project that is close to our hearts
Behind K-loop are enthusiastic and committed teams who have worked together to create the most rigorous process possible. Each of the experts has specific know-how, and together they are like links in a chain: it is when everything fits together that a well-structured project comes into being. None of this would have been possible without the tenacity of our employees and the project’s partners!
One of these experts is Matteo Borri, brand manager at KARIBAN BRANDS and creator of the Kimood brand. This nature lover with a profound respect for human values strives to give a profound meaning to his work, throughout the design of Kimood products.
His unwavering commitment is reflected in the very DNA of the K-loop project.

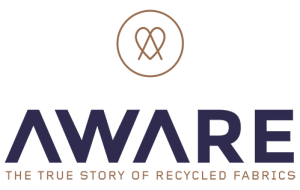
Together with this, Aware technology was the perfect partner for making these actions verifiable, not only because it is an independent organisation, but also because its values of transparency and honesty were essential for the project. With Aware it is now possible to certify that this is a truly and objectively environmentally responsible process.
The KARIBAN BRANDS teams, together with those of the TopTex Group, have constantly sought the most suitable and effective solutions, to achieve the precise and carefully thought-out result that we are proud to be able to present to you today!
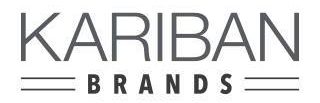
To limit our environmental impact, together
Within the TopTex Group, we are fully aware that as players in the textile industry, we have more than ever a role to play in saving resources and protecting our environment.
The KARIBAN BRANDS teams have worked tirelessly to analyse, correct and optimise each step in the K-loop cycle. And together, we will always continue to challenge ourselves, and make adjustments so that our efforts are rewarded with ever more positive outcomes.
It is already very gratifying to be able to say that the K-loop production process has a real, quantifiable impact. Details for a single KI5808 bag designed using this method:
- Recycled materials: 73% recycled cotton, 25% recycled polyester and 2% other fibres from fabric scraps from KARIBAN BRANDS products
- Water saved: 1,048 litres of water that will not be used to produce and grow cotton or to dye it a new colour
- Land preserved, and carbon emissions avoided: 0.000061 hectares of land not damaged by pesticides, and 0.8 kg of CO2 not emitted
- Waste recovered and reduced: 3.6 50 cl plastic bottles that will not end up in our seas, and 0.18 kg of waste not produced due to the recovery of existing materials
All this without losing sight of the quality objective – to offer you a tote bag with an ideal capacity and a pleasant, strong fabric.
We have taken you through the K-loop recovery process, to show you every detail, every step and everyone involved in the process in the most transparent and comprehensive way possible. From the involvement of the teams to the quality of our partners, and including the technical and logistical aspects, we are proud that this project has come to fruition, and we will continue to be involved in optimising it over time.
The K-loop was launched in 2022 and is now running continuously. We look forward to enhancing and improving it further, to extend this manufacturing process to other items in the TopTex Group. And at KARIBAN BRANDS, new K-loop products are currently being developed and should be available very soon!
So we are even more determined to prioritise recycling and recovery over the coming years, and to combat the waste of materials and resources. Just as we will always make it a point of honour to ensure that our teams and our partner factories have safe and healthy working conditions, while respecting people without discrimination.
For all these reasons, the K-loop project resonates more than ever, in a world where sustainable development is everyone’s duty, and where every step contributes to the collective effort.
One thing is certain: we will try to do better than yesterday, to help make tomorrow’s world better!